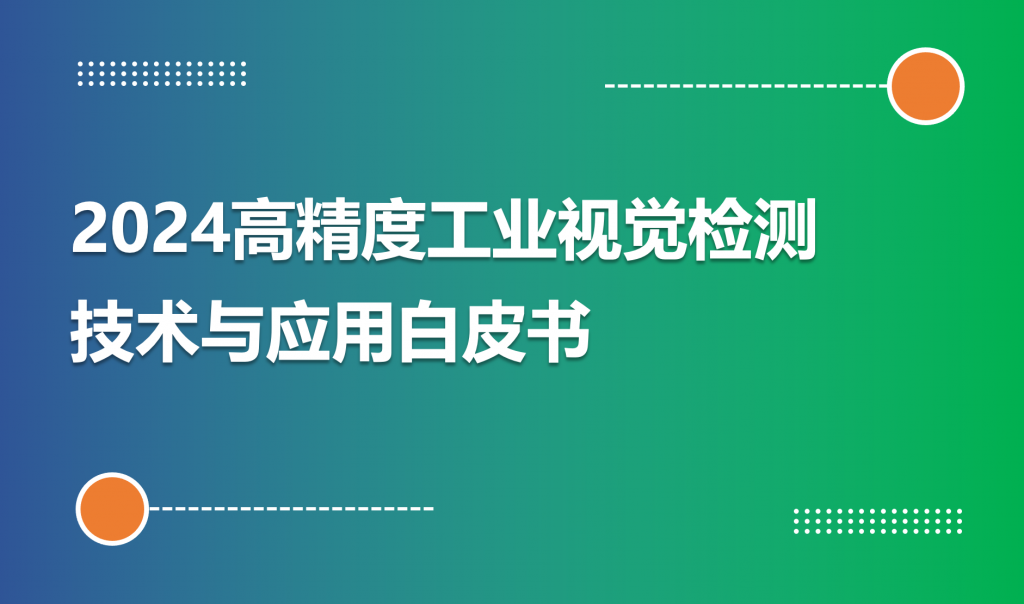
一、引言
随着工业发展进入智能时代,高精度工业视觉检测技术作为智能制造的核心技术之一,对于提升制造业的质量和效率具有至关重要的作用。本白皮书由中国移动通信有限公司研究院牵头,联合多家单位编写,系统地介绍了高精度工业视觉检测技术的发展现状、关键技术、应用案例以及未来展望。
二、高精度工业视觉检测发展概述
(一)发展现状
- 底层技术进步推动
- 图像采集技术:多视角、多光谱成像技术发展,多相机系统与灵活可调光源设计成为主流,超高分辨率相机和先进光学镜头应用提升缺陷检测能力。
- 图像处理技术:传统机器学习算法被深度学习的 AI 算法替代,推动算力需求增加,促使图像处理硬件设施升级,同时云边协同和 5G 技术拓展算力空间。
- 硬件技术:三维视觉和实时建模技术成熟,自适应路径规划应用增加,高自由度机械臂等技术提升执行机构灵活性和精确性。
- 市场需求增长拉动
- 机器替人:机器视觉相比人类视觉有优势,且劳动力短缺和成本上升推动机器替代人进行检测。
- 智能决策支持:AI 向工业制造全流程渗透,带动高精度工业视觉检测技术需求。
- 柔性化生产:个性化定制和小批量、多品种生产趋势,要求视觉检测系统更具灵活性。
(二)面临挑战
- AI 技术应用相关
- 工业视觉研发与实施环节加长,涉及模型训练等多个方面,本地方式面临算力瓶颈等问题,需做好本地与云的协同。
- 数据问题
- 数据采集不足,企业过去不重视数据留存,且采集源分散,同时数据没打通,格式不一致,限制了技术的产业化发展。
- 检测场景变化
- 制造企业混线生产,产品种类和型号多样,缺陷大小各异,视觉检测算法泛化性能和检测精度面临挑战。
- 工业装备协同
- 传统视觉检测设备功能单一,缺乏灵活性和扩展性,难以满足多样化生产需求,需增强交互及协作效率。
三、高精度工业视觉检测关键技术
(一)云边端一体化协同
- 架构优势
- 采用 “管理中心 (云)+ 生产中心 (边)+ 生产节点 (端)” 多级协同架构,融合 5G、人工智能等技术。云端提供算力和知识库,边缘站点进行数据汇聚和模型推理,端侧执行数据采集和推理。
- 应用效果
- 可满足不同规模企业需求,大型企业可按集团、园区、产线划分云、边、端,小型企业可云边合设。同时能实现云中训练、本地推理,满足数据安全需求,还可方便地进行模型按需分发和自动部署运行,以及打通各点位连接,提升管理效率。
(二)柔性化标准数采技术
- 现有问题及解决方案
- 现有的数采技术存在数据质量鲁棒性差等问题,构建 “柔性化标准数采方案”,包括光源方案、成像点位自主规划、数据扩充和数据评估。
- 各部分具体内容
- 光源方案:采用环形光源和波长适配的成像方案,搭配特定相机和镜头设计,可突出缺陷信息,满足不同工件成像需求。
- 成像点位自主规划:由工业镜头组和机械臂组成数据采集方式,基于 3D 扫描或工件模板数据规划自动拍摄路径,确保无死角图像采集。
- 数据扩充:采用传统数据增强方法和基于多模态大模型的数据离线增强方案,解决缺陷样本数量不足问题。
- 数据评估:引入基于 Transformer 的光学评价算法,建立图像特征与质量评价结果的关系模型,选取合适硬件参数设置方案。
(三)高精度视觉检测算法
- 解决行业痛点的策略
- 从多模态信息融合、无监督小样本学习与数据增强、多尺度级联的特征融合增强等技术入手,突破工业视觉算法瓶颈,同时将视觉检测系统模块化,提供定制化解决方案,利用领域自适应技术缓解场景泛化性低的问题。
- 不同技术应用案例
- 多模态信息融合:在五金保温杯和服装成衣缺陷检测中,通过不同方式融合多模态信息,解决数据采集和缺陷分辨等难点。
- 无监督小样本学习与数据增强:在汽配轮毂、纺织裁片和服装成衣缺陷检测中,利用相关技术解决数据稀缺等问题,提升检测能力和算法性能。
- 多尺度级联的特征融合增强:在汽配轮毂、五金保温杯和服装成衣缺陷检测中,通过不同策略提升缺陷检出及召回能力。
(四)人机交互与多机协同
- 人机交互技术提升体验
- 多模态人机交互技术融合专家与机器能力,提升认知决策能力,操作人员可通过整合视觉、文本、语音等信息与生产系统交互,准确把握产品设计细节和公差范围。
- 多机协同提高效率
- 多机协同结合多种技术,实现人机协作等,提高生产效率、产品质量和安全性,通过分析任务需求协调机器间任务分配和结果汇总,还可进行根因分析挖掘,提升生产工艺质量。
四、高精度工业视觉检测应用案例
(一)汽车行业轮毂表面缺陷检测
- 场景需求
- 轮毂生产企业虽部分环节自动化,但终检外观检测仍依赖人工,存在工作强度大、缺陷识别效率低和漏检等问题,需要研发适配各分工厂的检测系统,检测多种混合缺陷,轮毂型号和缺陷类型多样、结构复杂且表面高反光。
- 方案实施
- 云边端一体:采用多级协同体系架构,集团中心远程监控,厂区管理工作流程和更新算法,产线端侧传感器监控设备状态,柔性化数采系统和高精度算法结合识别缺陷。
- 柔性化数采:利用轮毂三维模型驱动机械臂进行视觉点位自主规划,实现全表面高清成像。
- 高精度算法:通过无监督异常检测进行小样本模型训练和迭代,结合人机协同技术约束决策边界,提高泛化能力。
- 应用成效
- 检测范围覆盖 14 类常见缺陷,准确率和召回率高,在浙江今飞试点应用后,大幅降低人力成本,预计 3 年内回本,还可迁移应用于其他汽车零配件检测。
(二)五金行业保温杯表面缺陷质检
- 场景需求
- 保温杯生产企业主要靠人工目检,存在结果不稳定和对工人身体有不良影响等问题,需求包括高精度、高效率、智能化检测以及数据记录与分析。
- 方案实施
- 云边端一体:采用两级架构,边缘节点管理生产线端侧算力设备和质检应用。
- 柔性化数采:采用高速 3D 视觉扫描成像等技术,实现对微小瑕疵的高清成像,设定检测周期并按频率拍摄。
- 高精度算法:采用多阶段级联缺陷检测算法,提高检测准确性和召回率。
- 人机交互协同:操作人员可实时接收检测结果并手动调整参数。
- 应用成效
- 可识别 6 类常见缺陷,检出率和准确率较高,在浙江匡迪工贸试点应用后,减少质检工人,节约人力成本,预计 1 年内回本,市场潜力巨大。
(三)服装行业成衣质检与裁片测量
- 场景需求
- 成衣质检需检查面料、颜色、图案等方面的瑕疵,裁片测量需精确测量关键尺寸并检查对称性等。
- 方案实施
- 柔性化数采:采用可调节 LED 光源、高分辨率相机和可互换光学成像组件。
- 高精度算法:在裁片测量采用自适应特征选择和模板匹配,在成衣缺陷检测采用重采样和重加权策略,提高检测精度。
- 应用成效
- 在海澜集团试点应用后,减少质检员数量,降低人工成本,提高测量准确性和稳定性,预计 1 年内回本。
五、展望与倡议
(一)发展方向
- 标准制定
- 在保持高度定制化的同时推进标准化进程,以实现快速部署和规模化应用。
- 数据驱动
- 利用大数据和深度学习技术挖掘和分析工业视觉数据,提高检测准确性和效率,通过算法训练和工艺改进识别更微小缺陷。
- 视觉技术
- 结合 2D、3D、多视角拍摄和多模态图像融合技术提升检测能力,发展具身技术提高自动化水平。
- 通信技术
- 融合 5G、云边协同等技术提高数据传输和处理速度,促进检测系统灵活部署,提升企业生产效率。
(二)合作倡议
- 中国移动研究院邀请工业视觉检测技术相关产业同仁携手合作,共同推进信息技术注智赋能传统制造业,助力企业转型升级等,为实体经济发展和新型工业化作出贡献。
六、结论
高精度工业视觉检测技术在当前工业发展中具有重要地位,虽然面临诸多挑战,但通过关键技术的不断创新和应用案例的实践验证,已经取得了显著的成果。未来,随着技术的不断发展和产业合作的进一步加强,有望在更多工业领域得到广泛应用,推动工业自动化和智能化水平的持续提升,为新型工业化和新质生产力的发展提供强大支撑。
商派官方订阅号
领取相关报告
近期文章
- 为何知名品牌认为“落地复杂难 IT 项目,商派更具优势”?——剖析商派在“复杂难”数字化项目交付中的竞争力
- Insta360影石创新市值突破1200亿元:90后技术极客刘靖康,用硬科技改写全球消费电子格局
- AI智能玩具赛道火热:ZTE中兴、索尼、字节跳动、乐森、萌友智能纷纷加码
- AI智能家电:技术革新重构生活方式——海尔、美的、格力依托制造优势,华为、小米发挥系统优势;华曦达、云米聚焦特定场景
- AI宠物的“数字温暖”,技术重构下的情感陪伴新物种!百度、小米、华为通过“硬件+AI生态”模式切入
- 童装与电商双轮驱动下的战略突破:361°集团2025年上半年营收达57亿元
- GENTLE MONSTER(GM眼镜)新加坡滨海湾金沙旗舰店焕新启幕:以空间叙事重构零售未来
- Songmont山下有松:一个国产轻奢包袋品牌的商业进化论
相关文章
产品推荐
- B2B/B2B2b/S2B2B数字化系统 经销商订货管理数字化解决方案